The role of work order management is crucial for every organization. Every systematic organization comprises coordinated tasks that have to be performed by various equipment. The absence of a repair and maintenance system in your business can lead to operational issues, wasted resources, and inefficiency. In this article, we will explore what work order management is and how it can be implemented in organizations to receive maximum business benefits.
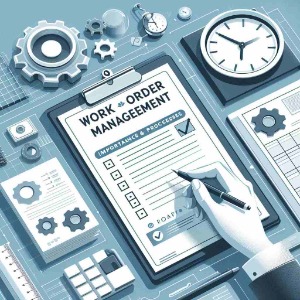
Table of Contents
What Exactly is Work Order Management (WOM)?
Work order management is the process of managing and organizing the company’s maintenance, repair work, and operational tasks. They must be addressed simultaneously to ensure each of them is addressed quickly and effectively. Work order completion relies on resources like assets, people, and money. To succeed in WOM, you will need trained professionals who can follow defined procedures and a robust system to automate the process of handling large volumes of work orders.
Why Do We Need a Digitized Work Order Management System?
In previous days, organizations relied on paper-based work orders to communicate tasks. Although creating work orders by hand was easier, the task was labor-intensive and also led to errors. Physical copies can easily get misplaced and finding historical work orders was a difficult job. Maintenance teams then moved to spreadsheet-based work order management. Again, this has its own limitations and can only be controlled by one person at a time.
Organizations had to grow from old-school ways of communicating and managing work orders. Businesses started using facility maintenance software to focus on operational efficiency and effective management of various aspects of the business including work order management. Through the software, users can initiate work orders by specifying task details and their priorities. The application will track the progress of the work order from start to finish. This way all the human work of documenting work orders and communicating through paper came to an end and the management of the organization’s tasks became much more efficient and error-free.
How Does the Work Order Management Process Work?
Each work order in the work order management is given consideration from the initial stage till its completion. Work order management processes include:
- Approval of Work Request:
A user communicates the requests for maintenance work through work request. The request is checked by the reviewer before creating a work order. Whether there is a legitimate need to cater to the request or if the issue was already reported. If the request is valid, it will get approved and a work order for the request will be created. - Creation of Work Order:
Once authorization is given for the request and the issue is identified, a work order request is created and submitted. The facilities are notified and the maintenance team prioritizes the task for completing it efficiently. As part of the process, it is necessary to provide every detail of the work to the maintenance technicians. - Approval and Priority of Work Order:
The manager then approves the work order before the work is initiated. This is to ensure that the requested work order is not already in process or is on the team’s to-do list. It is also essential to identify the priority level of the request if not specified by the request initiator. - Assigning the Work Order to a Technician:
If your system does not assign the work orders to technicians automatically, it is essential to assign the task to the right technician manually. While assigning one must keep in mind the technician’s workload and expertise. - Execution of the Work Order:
Once the work order is assigned, the technician can focus on executing the work order. Technicians have to adhere to all safety protocols and guidelines that are given for repairing equipment. - Documentation:
The training workers of the work order have to document all results either good or bad. They are supposed to record everything that was done, what parts were used, and how much time it took. - Closing of Work Order:
Once all tasks are complete and all services delivered the technician’s job is complete. Now they are available to work on other work orders. - Review and Follow Up on the Work Order:
Once the equipment is fixed by the technician, it is important to review it. Follow-up is also needed to inspect the equipment and make sure it stays up and running.·
Best Practices to Work Order Management:
To get the maximum benefits through work order management, teams have the following things in common:
- Clearly defined goals, process and responsibilities
- They work on improving their internal processes
- Use maintenance software to streamline and automate work
- They focus on their maintenance teams well-being
Benefits of using a Digitized Work Order Management System:
An efficient work order software system leads to many benefits:
- It streamlines your maintenance procedures and eliminates paperwork.
- It creates a centralized space to assign, schedule, and track working labor hours
- It tracks maintenance performance
- Keeps an estimation of labor, parts, and other costs and pricing
- Helps in managing the company’s inventory such as ordering parts and supplies so work order is completed on time
- Maintains regulatory compliance and helps avoid fines
Final Thoughts:
Incorporating work order management into an organization can automate and centralize the processes of maintaining and repairing. This integration leads to better resource utilization, improved efficiency, and an organized approach to facility management.